Speeding up the journey
ENRX is a new brand with decades of experience in induction heating, wireless inductive charging and contactless power supply. We speed up the journey to a sustainable world through smart energy transfer within manufacturing and mobility. Need to speed up your journey? We are ready when you are.
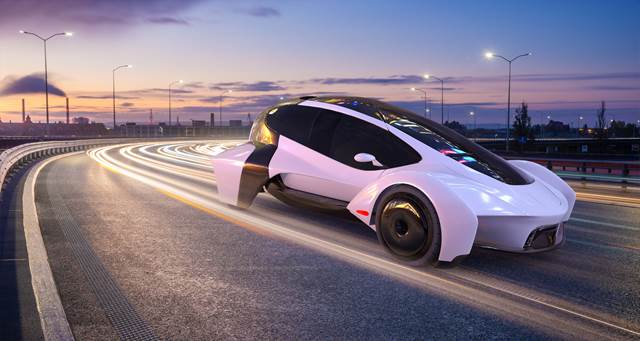
The right energy can take you anywhere
The only limit for wireless transfer of energy is your imagination.
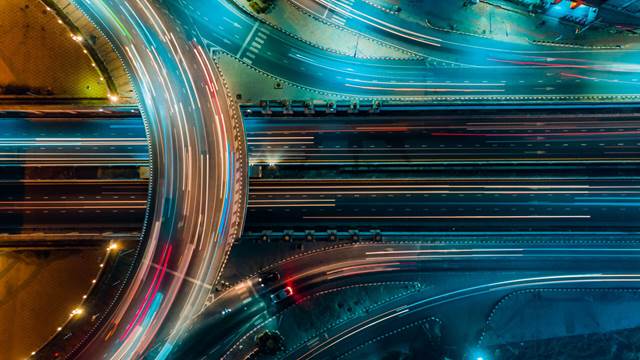
When people look back, they will find that we were years ahead
Our vision moves us forward as a company; we hope it moves you too.
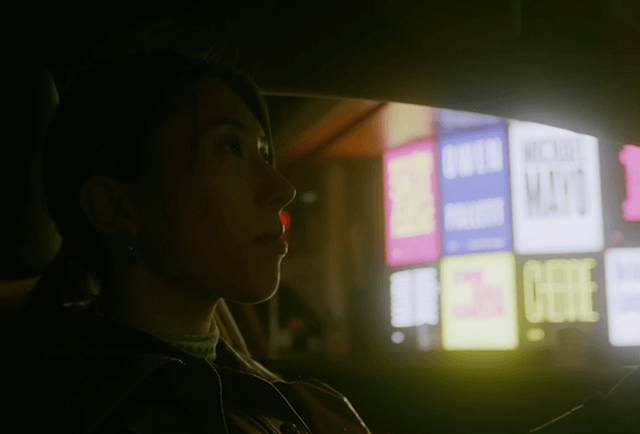
Sustainability and annual report 2023
One year after the launch of the new company, we can look back on a record breaking 2023. ENRX became a true success – a real powerhouse in induction technology, ready to speed up the journey in 2024.
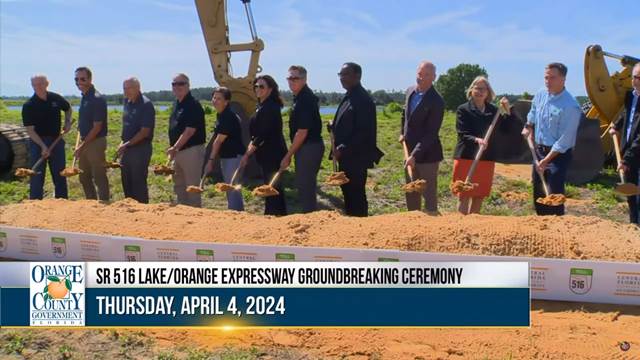
Breaking ground on trailblazing new expressway
It was spades in the ground yesterday as representatives for all involved in the new State Road 516 in Florida gathered to celebrate the start-up.
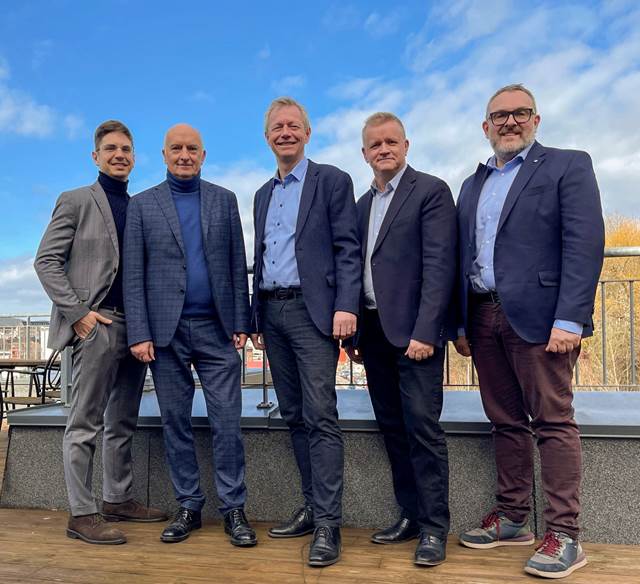
Working together towards wireless charging
We are happy to announce that ENRX has entered into a strategic cooperation agreement with the Italian company, R.M. Sistemi Elettronici S.r.l.
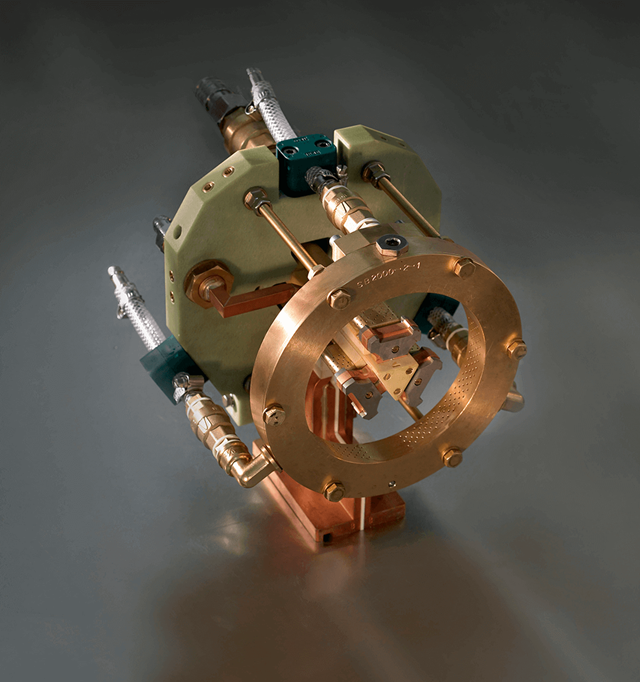
The heart of your machine
Find out in a minute if you need a conventional, machined, 3D or hybrid coil.
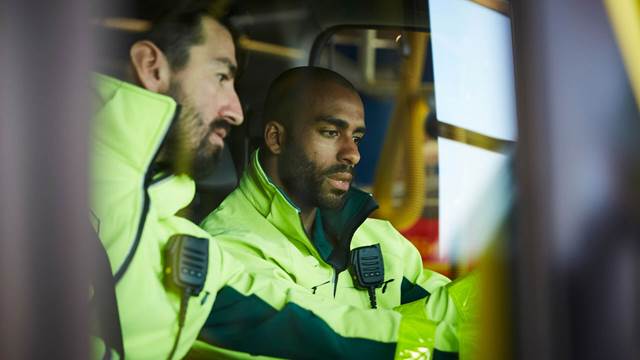
What can we do for you?
Our wide range of services keeps your equipment or system up and running.
.jpg?mw=640&mh=1024)
Thrive at work every day
No yawning – just laughter, optimism and a strong belief in the future.
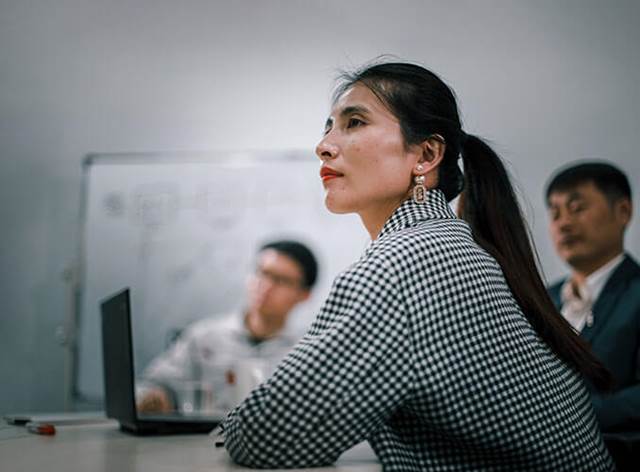
Insights from all over the world
Stay up to date with the latest news from ENRX.